Эта статья о сборке механической части 3D принтера RepRap Prusa Mendel. В ней будет описана сборка каркаса, установка двигателей, каретки, подвижного стола и т.п. Все что касается электронной части будет описано в следующей статье.
Сразу оговорюсь, что я не буду давать детальных пошаговых инструкций по сборке принтера. Во первых, это уже сделано до меня. Во вторых, подобные инструкции могут существенно отличаться в зависимости от комплектующих и конкретной модели принтера (например, если у вас комплект пластиковых деталей для Prusa Mendel iteration 2, то инструкции для iteration 1 вам не совсем подойдут). Вместо этого, я постараюсь описать процесс сборки в целом, а также некоторые трудности и подводные камни, с которыми столкнулся я сам.
Детальные инструкции по сборке можно найти на
сайте проекта RepRap, например
здесь (Prusa Mendel Iteration 1) и
здесь (Prusa Mendel Iteration 2). Но т.к. RepRap является открытым, поддерживаемым сообществом проектом, то даже на официальном сайте (Вики) нередко можно найти ошибки, опечатки, и просто куски скопированной несогласованной информации. Поэтому здесь как нельзя кстати поговорка про "семь раз отмерь, один раз отрежь", так что перед тем как что-нибудь делать, не поленитесь перепроверить размеры лишний раз.
И на всякий случай напомню, что модель принтера которую собирал я - RepRap Prusa Mendel Iteration 2 (с небольшими изменениями), поэтому все размеры описанные в статье относятся только к ней.
Каркас (frame)
Каркас принтера состоит из стержней с резьбой диаметром 8мм, скрепленных с пластиковыми деталями с помощью гаек M8. Прежде чем начать собирать каркас нужно нарезать стержни до нужной длины (обычно стержни продаются кусками длинной в 1м, и легко режутся обычной ножовкой по металлу). Всего нужно 15 стержней:
- 6 стержней для боковых треугольных рамок (frame triangles).
- 2 верхних стержня, на которые крепятся моторы оси Z (top rods).
- 4 нижних стержня - два передних и два задних (lower rods for front and back side).
- 1 нижний центральный стержень, к которому крепятся направляющие оси Z (low center rod).
- 2 стержня которые используются как червяки для перемещения каретки по оси Z (Z rods).
Первым делом собираются две боковых треугольных рамки:
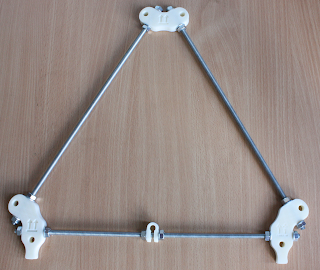 |
Боковая треугольная рамка |
На этом этапе не стоит затягивать гайки, пусть все свободно болтается, выравниванием каркаса и затягиванием гаек займемся позже.
Далее, нужно подготовить пару передних и пару задних стержней, которые скрепят треугольные каркасы.
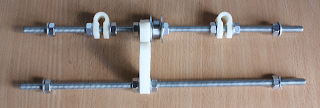 |
Передние стержни |
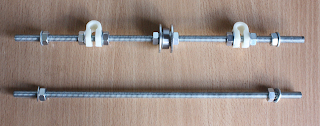 |
Задние стержни |
Скрепляем две треугольных рамки с помощью этих пар стержней:
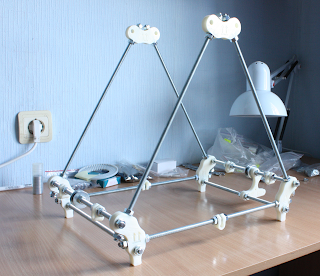 |
Скрепление треугольных рамок |
Устанавливаем два верхних стержня с площадками под моторы:
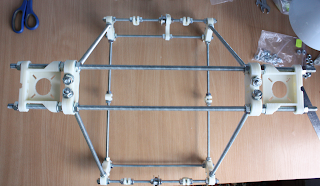 |
Установка верхних стержней |
Теперь нужно установить нижний центральный стержень, но перед этим сделаю небольшое отступление. Есть два очевидных варианта установки этого стержня - снизу и сверху. Обычно вариант "снизу" более предпочтителен, т.к. стержень будет дальше от ремня, приводящего в движение стол. Однако, я был вынужден выбрать вариант "сверху", т.к. длины имеющихся у меня направляющих стержней для оси Z было недостаточно для варианта "снизу". Ремень оси Y действительно касается центрального нижнего стержня, но трения практически не возникает, поэтому не думаю что это является проблемой.
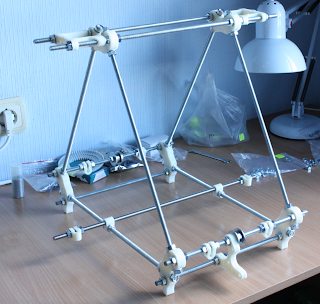 |
Установка центрального нижнего стержня |
Теперь самое время выровнять каркас и затянуть гайки. Подробно этот процесс описан в вики RepRap как
Tightening The Frame. Если вкратце, суть его состоит в коррекции (с помощью гаек) расстояний между вершинами боковых треугольников, и между самими треугольниками, так что бы оно максимально точно соответствовало необходимому. Что бы не возиться с линейкой, лучше заранее заготовить два куска деревянной реи (или чего-то другого, главное - прямого) необходимой длины (в RepRap Wiki эти приспособления называют jigs). Один будет использоваться для измерения расстояния между вершинами треугольников, второй - между самими треугольниками. Торопиться с этим процессом не стоит, т.к. кривой каркас может доставить много проблем.
Устанавливаем направляющие стержни оси Y. Если у Вас есть подшипники типа LM6UU то не забудьте одеть их на стержни перед установкой.
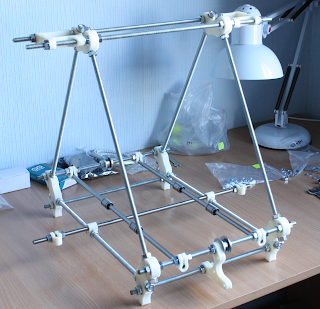 |
Установка линейных направляющих оси Y |
Далее, необходимо собрать ось X. Сначала крепим подшипник к детали, которую обычно называют "X end idler":
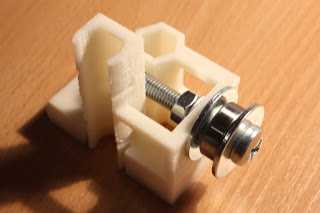 |
X end idler с подшипником |
И одеваем X end idler и X motor holder на направляющие стержни (не забываем про подшипники):
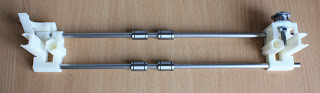 |
Сборка оси X |
Теперь нужно собрать ось Z. Сперва необходимо выровнять принтер и центральный нижний стержень. Детально этот процесс описан, например,
здесь, поэтому опишу только в двух словах.
С помощью строительного уровня подкладывая кусочки бумаги под ножки устанавливаем принтер полностью горизонтально (в двух плоскостях, не в одной). Далее, с помощью отвесов выравниваем центральный стержень оси Z так, что бы нить отвесов проходила точно через центры хомутов:
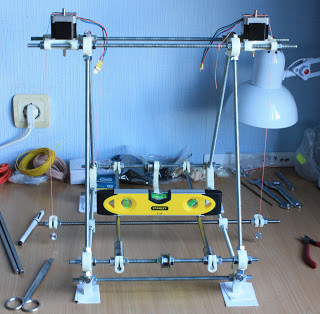 |
Сборка оси Z |
Теперь продеваем направляющие оси Z через подшипники оси X, и крепим их с помощью зажимов (сверху) и хомутов (снизу):
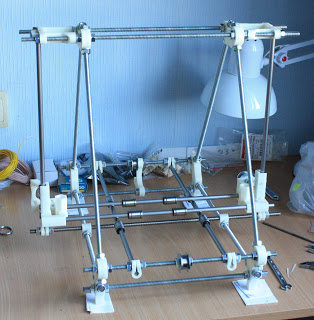 |
Сборка оси Z |
Следующий шаг в сборке оси Z - установка двигателей. Здесь есть небольшой нюанс: т.к. стержни с резьбой, которые используются как червяки для оси Z, могут быть не идеально ровными - при вращении их может заклинить. Что бы этого избежать я установил двигатели не жестко, а на небольших шайбах из шланга для аквариума (прозрачный силиконовый шланг диаметром около 5мм). Это дает двигателям немного свободы, и таким образом предотвращает заклинивание.
После установки двигателей нужно установить на место червяки оси Z. Процедура следующая (она одинакова как для X end idler так и для X motor holder, я опишу на примере X end idler): помещаем гайку снизу в шестигранный канал X end idler, сверху в шестигранный канал кидаем пружинку, и на нее кладем еще одну гайку. В верхнюю гайку вкручиваем стержень (который будет играть роль червяка), сжимаем пружинку с небольшим усилием,и продолжаем вращать стержень до тех пор, пока он не пройдет сквозь нижнюю гайку. Таким образом, пружина останется в немного напряженном состоянии, это помогает устранить нежелательный люфт.
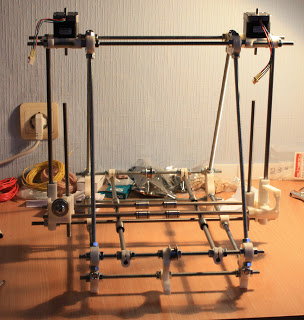 |
Сборка оси Z |
Последний шаг это соединение червяков с валами двигателей. Муфты, которые используются для этой цели, бывают разных конструкций. Мне достались вот такие:
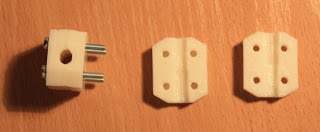 |
Муфта для оси Z |
Но ставить муфту на голый металлический вал не стоит, т.к. коэффициент трения у пластика с металлом небольшой - возможно проскальзывание, а оно приведет к очень плохим последствиям. Поэтому конец червяка я покрыл тонким двусторонним скотчем, а на вал двигателя одел все тот же шланг для аквариумов, предварительно нагретый с помощью фена.
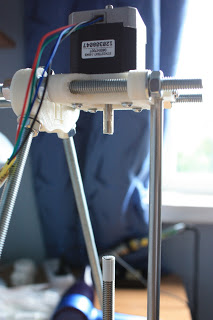 |
Соединение червяка оси Z и вала двигателя |
На этом сборка оси Z завершена:
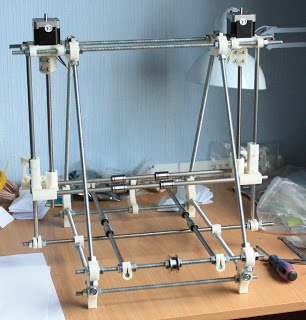 |
Сборка оси Z |
Осталось немного: установить двигатели осей X и Y, установить каретку, и натянуть ремень оси X. Ремень нужно натягивать так что бы он не провисал и не было люфта каретки, но, в то же время, натяжение ремня не должно затруднять движение каретки.
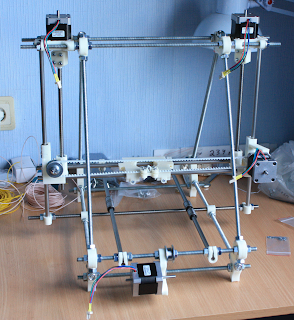 |
Установка каретки, двигателей, и натяжение ремня оси X |
На этом сборка каркаса завершена.
Здесь я ничего не упомянул про сами двигатели, но они будут описаны в следующей статье, посвященной электронике RepRap.
Стол с подогревом для печати
В простейшем варианте стол для печати (print bed) может представлять собой квадратный лист металла или стекла, перемещающийся на подшипниках по направляющим оси Y, и приводимый в движение шаговым двигателем с помощью ременной передачи. Но, как правило, стол делают "двухэтажным". Первый "этаж", обычно выполненный из дерева, МДФ или композитных панелей, жестко закреплен на подшипниках. Второй этаж, на котором, собственно, и идет печать, удерживается болтами и пружинами над первым.
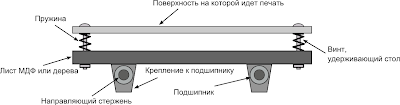 |
Подвеска стола |
Такая подвеска позволяет легко варьировать высоту стола, а также выравнивать его положение относительно сопла экструдера.
Теперь о том зачем нужен подогрев стола. В RepRap Wiki подогрев стола представлен как необязательное улучшение, но я бы настоятельно рекомендовал его использовать, т.к. добиться приемлемого качества печати без подогрева стола может быть очень тяжело.
Подогрев стола необходим по двум причинам. Во первых, он повышает адгезию пластика к поверхности стола. Первый слой модели печатается прямо на поверхности стола, и необходимо что бы горячий пластик хорошо приставал к поверхности стола, а не тянулся за соплом экструдера. К нагретой поверхности пластик пристает существенно лучше чем к холодной. Во вторых, подогрев стола позволяет уменьшить разницу температур в разных частях печатаемой модели, и, таким образом, предотвратить её деформацию. Дело в том, что при печати модели (особенно большой) на холодном столе, её нижние слои начинают остывать еще до завершения печати (когда верхние слои еще горячие), а это приводит к тепловой деформации и выгибанию модели. При использовании подогрева стола температуру модели можно поддерживать высокой до завершения печати, после чего модель сама постепенно остынет, целиком.
Существует множество конструкций стола с подогревом, с некоторыми из них можно ознакомиться
здесь. Самой популярной считается конструкция где в качестве нагревательного элемента используется специальная
печатная плата, а в качестве поверхности для печати - стеклянный лист. Но мне такая конструкция не нравится. Во первых, такую печатную плату довольно тяжело изготовить в домашних условиях и от её качества сильно зависит равномерность нагревания, и то будет ли она греть вообще (т.к. сопротивление дорожек должно быть строго определенным, будет меньше - может сгореть блок питания, будет больше - не будет достаточно нагреваться). Во вторых, стекло - не самый подходящий материал для поверхности стола для печати, оно хрупкое, его легко разбить, да и от перепадов температуры оно может легко расколоться. Кроме того, стекло обладает плохой теплопроводностью, да и обеспечить хороший контакт между стеклянной пластиной и печатной платой - тоже непростая задача. Ну и в третьих, один из компонентов текстолита - эпоксидная смола - не самый полезный продукт, особенно при нагревании.
Немного поэкспериментировав, я остановился на следующем варианте. В качестве поверхности на которой идет печать я использовал лист алюминия толщиной в 3мм:
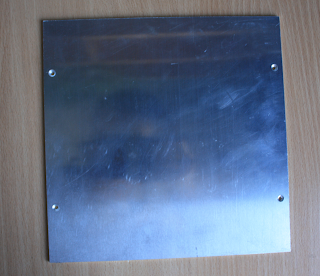 |
Алюминиевый лист с отверстиями под винты. Толщина 3мм. |
Помимо очевидных преимуществ по сравнению со стеклом, таких как прочность, алюминий также обладает теплопроводностью на два порядка выше чем у стекла.
В качестве нагревательного элемента используются резисторы в алюминиевом корпусе (aluminium clad resistor):
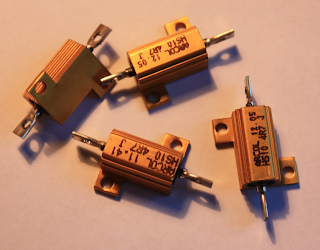 |
Резисторы сопротивлением в 4.7 Ом |
Обычно стол нагревают током в 10 ампер при 12 вольтах напряжения. Поэтому для нагрева стола можно взять 4 резистора емкостью в 4.7 Ома подключенных параллельно. Конкретно я использовал
вот эти резисторы. Т.к. пайка алюминия это очень непростая задача, то для крепления резисторов к алюминиевому листу я использовал теплопроводный клей "Радиал", выдерживающий температуру до 300 градусов и, по заверениями производителя, не токсичный. Им же в центр стола приклеен термистор B57560G1104F.
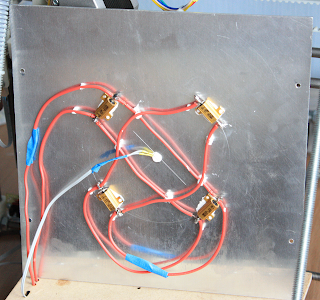 |
Стол с подогревом |
Есть небольшой нюанс с креплением проводов к резисторам. В процессе работы контакты резисторов могут нагреваться до температуры выше 200 градусов, поэтому если провода к ним просто припаяны обычным припоем - они отвалятся. Тугоплавкого припоя у меня не было, поэтому я использовал смесь скрутки и пайки - провода продеты в отверстия в контактах резисторов, скручены, и пропаяны. При нагревании припой размягчается, но провода не отваливаются, а припой обеспечивает хороший контакт.
Нижний "этаж" стола представляет собой лист MDF толщиной около 6мм. Как оказалось, купить MDF розницу у нас невозможно. Зато можно купить MDF панель для облицовки, снять рисунок, отшлифовать, и получить аккуратный кусочек MDF:
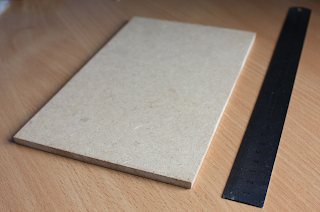 |
Кусок MDF для стола |
После вырезания MDF нужных размеров нужно просверлить в нем отверстия для второго этажа стола, для крепления подшипников, для крепления ремня, флажка концевика оси Y (если вы используете оптический концевик), и отвода проводов. Непосредственно перед установкой нижнего этажа стола нужно обязательно выровнять направляющие оси Y так что бы они были строго параллельны друг другу.
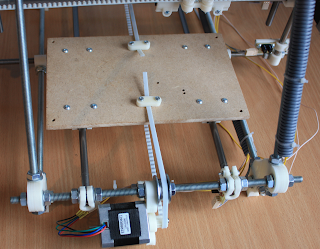 |
Установка стола на направляющие |
Теперь крепим флажок для концевика (я для вырезал флажок из текстолита, и прикрепил его на кронштейне из стальной проволоки):
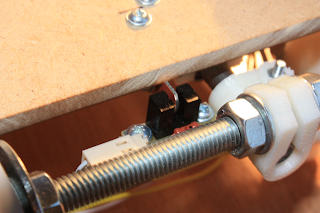 |
Флажок для оптического концевика оси Y |
И устанавливаем сверху, на пружинках, алюминиевый лист с резисторами:
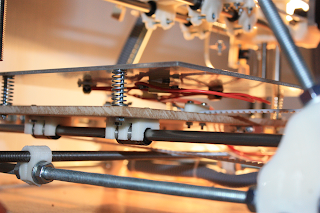 |
Стол с подогревом |
На этом пока работа над столом с подогревом завершена.
Экструдер
Экструдер является одним из самых важных компонентов, и, наверное, больше всего влияет на качество печати. Условно его можно разделить на две части: холодную (cold-end) и горячую (hot-end). Задачей cold-end является дозированная подача пластикового прутка в hot-end. А hot-end, в свою очередь, плавит этот пруток и выдавливает расплавленный пластик тонкой струйкой через свое сопло. Вариантов экструдеров очень много, некоторые можно посмотреть
здесь и
здесь.
В основном экструдеры рассчитаны на использование пластикового прутка диаметром 3мм или 1,75мм. Какой диаметр прутка лучше я затрудняюсь ответить. Сам я использую 3мм, поскольку его обычно проще достать. Главное - будьте внимательны и подбирайте cold-end и hot-end для прутка одного диаметра (3 или 1,75 мм). Если поставить hot-end рассчитанный на пруток 1,75 на cold-end рассчитанный на пруток 3мм - работать это не будет.
Итак, начнем с cold-end. Как я говорил, вариантов масса, но принцип везде используется один и тот же: шаговый двигатель через редуктор вращает вал с зубцами, к которым пружиной прижимается пластиковый пруток. Зубцы врезаются в пруток и при вращении вала проталкивают его в hotend. На момент написания этой статьи самым популярным был
Wade's Geared Extruder, и его улучшенная модификация -
Accessible Wade's Extruder (также именуемая Greg's Accessible Extruder). В мой комплект пластиковых деталей входил именно Greg's Accessible Extruder, поэтому и использовал я его. Он состоит из четырех пластиковых деталей (которые можно напечатать), также вам понадобятся три подшипника типа 608ZZ, небольшой (длиной около 1,5см) кусок стержня с резьбой, диаметром 8мм, болт с зубцами диаметром 8мм (о том как его сделать читайте ниже), гайки и шайбы M8.
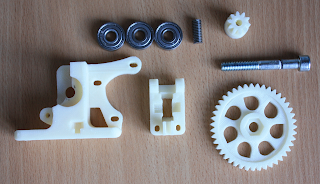 |
Детали cold-end части экструдера |
Теперь подробнее о болте с засечками (hobbed bolt). Его можно купить в магазинах комплектующих 3D принтеров, или сделать самостоятельно. Второй вариант мне кажется более разумным, т.к. болт имеет срок службы (засечки стираются), и лучше бы уметь делать болты самостоятельно, что бы без проблем менять их по мере надобности. Засечки можно нанести разными способами, о некоторых можно прочесть
здесь. Самое главное - соблюдать технику безопасности при работе с инструментами, а особенно - с дрелью!
Я наносил засечки следующим способом. Сперва закрепил болт в дрели (как сверло), включил дрель, и приложив кусок старого полотна от ножовки по металлу, сделал небольшую царапину, глубиной где-то в 0,3мм. Затем, приложив к этой царапине круглый надфиль во время вращения дрели, сделал канавку, глубиной около 1,5мм. После этого, я зажал в тисках два подшипника 608ZZ на расстоянии примерно 3-4см друг от друга, вставил в них болт с канавкой, закрепил его гайкой, и прижал к канавке метчик диаметром 3мм который вставлен в дрель в качестве сверла (дрель была включена до прижимания метчика к канавке, в противном случае она сильно вырывается из рук при включении). Вращение метчика приводит к вращению болта и нарезанию аккуратных зубцов:
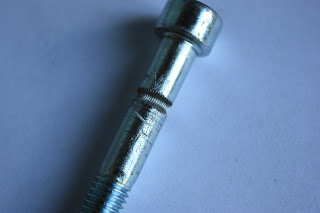 |
Болт с засечками |
Когда болт готов остается только собрать cold-end:
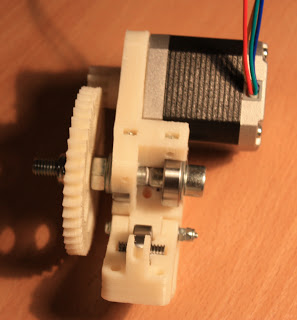 |
Собранный Greg's Accessible Extruder (в открытом виде) |
Теперь перейдем к hotend. С ними все намного разнообразнее - они сильно отличаются конструкциями, используемыми материалами, наличием или отсутствием активного охлаждения и т.п. Условно hotend можно разделить на четыре части (хотя некоторые части бывают объединены):
- Крепление к cold-end. Это та часть за которую hotend крепится к каретке или cold-end. Иногда на эту часть устанавливается пассивное (радиатор) или активное (куллер) охлаждение, во избежание плавления пластиковых деталей каретки или экструдера.
- Термобаръер (thermal break). Часть предназначенная для минимизации передачи тепла от нагревательного элемента вверх по hotend-у (к экструдеру). Часто изготавливается из PTFE (тефлон) или PEEK.
- Зона плавления (или зона перехода, или нагревательный блок). Часть hotend в которой происходит плавление пластика. Обычно представляет собой металлический блок с резистором в качестве нагревательного элемента и термистором, для контроля температуры.
- Сопло (nozzle). Обычно коническая деталь из металла, с отверстием из которого выходит расплавленный пластик. Диаметр отверстия сопла варьируется от 0,2 до 0,5 мм. Более предпочтительным является диаметр в 0,3-0,4 мм.
Рассматривать все варианты hotend-ов я не буду, на это нужна как минимум отдельная статья (с некоторыми вариантами можно ознакомиться
здесь). Расскажу только про два варианта.
Есть класс hotend-ов в конструкции которых используются только металлические детали (обычно их называют all metal hotend). Представителями этого класса являются, например,
E3D Hotend и
Arcol Hotend. Как мне кажется, подобные hotend-ы наиболее перспективны: они более надежны, могут выдерживать более высокие температуры, и не содержат PTFE или PEEK в своей конструкции. Последнее для меня особенно важно, поскольку PTFE при нагревании выше 200 градусов выделяет токсичные соединения в воздух (но это не является проблемой если вы собираетесь печатать только PLA, температура плавления которого около 180 градусов).
Второй класс hotend-ов называется
J Head. На самом деле это всего лишь разные версии одного hodend-а, но их настолько много что сейчас J Head это скорее некий класс hotend-ов. Конструктивно J Head устроен достаточно просто - нагревательный блок объединен с соплом, и выполнен в виде цельнометаллического куска фрезерованного из латуни или алюминия. Внутрь обычно вставляется трубка из PTFE (liner), с целью уменьшения трения прутка о стенки и предотвращения его преждевременного плавления. Термобаръер и крепление к cold-end тоже объединены и выполнены из PEEK. На момент написания этой статьи J Head был самым распространенным и проверенным hotend-ом, и отчасти поэтому я выбрал его (если быть точнее -
J-Head Mk V-B). Для крепления к каретке я использовал вот
это крепление фрезерованное из куска алюминия.
В качестве нагревательного элемента в hotend обычно используется резистор сопротивлением 5.6 или 6.8 Ома и мощностью 3-5 Ватт. В качестве термистора я использовал все тот же B57560G1104F.
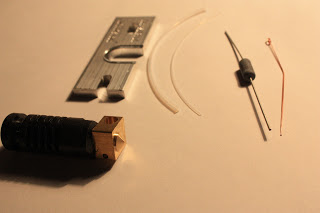 |
J-Head, крепление, резистор, термистор, трубки из PTFE для изоляции |
Собрать hotend несложно. Сперва приклеиваем на место резистор и термистор (я использовал все тот же теплопроводный клей Радиал). Затем одеваем изоляцию в виде PTFE трубок. На выводы резистора и термистора я обжал клеммы типа BLS и склеил их между собой.
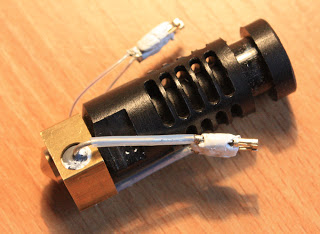 |
Собранный J Head |
Устанавливать hot-end и cold-end пока не нужно, сперва нужно будет откалибровать подачу прутка (об этом я напишу в следующих статьях).
Заключение
На этом пока всё. Следующая часть будет посвящена электронной части RepRap, а именно - управляющей плате, двигателям, концевикам (endstops), блоку питания и подключению всего этого. Возможно, такой стиль изложения выглядит несколько непоследовательным (ведь в этой статье я использовал двигатели, о которых речь пойдет только в следующей статье), но он мне кажется более структурированным и наглядным. Если о чем-то нужно рассказать более подробно - пишите в комментариях.
12 комментариев:
Блін, це круто! Просто чудовий цикл! Ці три статті виявилися надзвичайно інформативними, та ще й читаються на одному дусі. З нетерпінням чекатиму на продовження.
Взагалі, натрапив на ваш блоґ, бо загорівся бажанням і собі скласти таку машинку. Вирішив саме скласти (а не купити) з метою економії. В мене таке уявлення, що можна зібрати робочу версію відносно дешево, а вже потім - вдосконалювати і доводити до більш придатного стану (доробити стіл з підігрівом і т.д.).
У зв'язку з цим хочу задати кілька запитань:
1. Чи має взагалі вищеописана точка зору право на життя? І якщо так, то у яку ціну ви би описали таку початкову версію? (зібрані продаються по $600, якщо не помиляюся, а хотілося би дешевше)
2. Чи не маєте ви раптом бажання роздрукувати для мене деталі на своєму принтері на взаємовигідних умовах?
Мысль здравая, безусловно, только учтите, что возможности для экономии весьма ограничены. Из самых дорогих деталей - двигатели, электроника, направляющие, хотэнд. Можно неплохо сэкономить на электронике (особенно если дружите с паяльником). Если удастся найти направляющие поблизости - тоже, наверное, выйдет дешевле (мне их пришлось заказывать). Хотэнд можно сделать самому, если есть доступ к токарному и фрезерному станкам.
Но, честно говоря, я думаю вряд ли получится сделать дешевле чем 400-500$.
Выбирая детали также не забывайте о стоимости доставки, т.к. иногда она оказывается выше стоимости самих деталей.
Распечатать детали, к сожалению, сейчас нет возможности. Но их найти не сложно, и весят они мало.
О, $400-500 - вже непогано.
Здивувало, до речі, що направляючі так проблемно знайти.
На рахунок електроніки - візьму до уваги, може й справді щось получиться. А от із хотендом, мабуть, не варіант.
Щодо деталей: знаю, що найти не важко, але мав надію обійтися малою кров'ю (у сенсі без виходу за кордон). Ну, таке, буду розбиратися :)
Дякую за швидку відповідь.
По поводу различных деталей советую заглянуть в русский раздел форума RepRap - http://forums.reprap.org/list.php?54 . Там можно и направляющие найти, и пластиковые детали.
Ага, і справді корисний ресурс
Приветствую
Как было определено место крепления резисторов к столу?
Anna She, для крепления резисторов я нацарапал циркулем окружность радиусом в 1/4 ширины стола (её хорошо видно на фото), и на неё с промежутком в 90 градусов наклеил резисторы. Чисто интуитивно такой способ размещения показался мне оптимальным, а практически пока возможности проверить нет, но проблем с равномерностью прогрева (warping) пока не наблюдал.
Тоже собирал принтер, только в качестве стола использовал MK2B Heatbed. Были сильные проблемы с нагревом - не мог нагреть выше 105 градусов. Проблема решилась покупкой мощного БП - но и с ним не удавалось нагреть выше 120 градусов, пока не догадался охлаждать силовые транзисторы ))) А так, подумать пришлось крепко.
Самая большая проблема - экструдер, не жалейте денег, материала (чего еще там) на него, а то потратите кучу времени, пытаясь заставить его работать
Греть выше 100-110 градусов панель смысла нет.
Тоже купил сначала в наборе принтера панель MK2B, нагрев отрубался из-за предохранителя, померял сопротивление - 0.7 Ома, ток превышал 11А термопредохранителя. Обратился к производителю, поменяли на MK1B, греет норм. Но наткнулся в прошивке на возможность настроить ток нагрева панели через ШИМ, теперь жалею что поторопился менять, можно было бы на 24В подключать для более быстрого нагрева.
Важно минимизировать сопротивление проводов нагрева стола - минимизируя падение напруги и общее сопротивление цепи нагрева. Между лишним метром тонкого провода и толстым проводом "только только в натяг" разница на прогрев измеряется минутами.
Да, и самое главное почему вероятно все нервно курят (кроме меня), ожидая прогрев стола - в магазе "все по 39р" купил кусок пробки и положил под панель, скорость нагрева возросла на порядок, без теплоизоляции до 105 градусов ждал по полчаса.
Еще можно накрывать стол каким-нибудь теплоизолирующим материалом (я использую кусок толстого гофрированного картона) - помогает немного сократить время нагрева.
Здравствуйте.
В статье вы верно указали, что тефлон выше 200 С выдедяет токсичные вещества, и изходя из этого подбирали себе хот-енд.
На сколько я понимаю, все хотенды снабжены тефлоновой трубкой внутри для предотвращения преждевременного подплавления прутка
" Внутрь обычно вставляется трубка из PTFE (liner), с целью уменьшения трения прутка о стенки и предотвращения его преждевременного плавления."
Хотел спросить, эта тефлоновая трубка вставляется на всю длину хотенда ( ну то есть она сама по себе нагревается выше 200 С) или по конструкции она до таких горячих мест не доходит?
еще вопрос-- вот целюсь купить у китайцев такой хотенд- что скажете
http://www.aliexpress.com/item/Free-Shipping-Metal-E3D-J-head-Hotend-Nozzle-0-2mm-0-3mm-0-4mm-3D-Print/2039801435.html
Но главный вопрос-- разогревается ли тефлоновая трубка до опасных температур?
Заранее спасибо
Трубка обычно вставляется практически на всю длинну, т.к. идея в том, чтобы пластик вообще не касался металла вплоть до самого сопла, где он плавится. До каких температур она нагревается - тяжело сказать, зависит от конструкции конерктного хотенда.
Я достаточно долго исследовал вопрос токсичности 3D принтера, и пришел к таким результатам:
- При печати PLA тефлон не опасен, т.к. он в принципе не может разогреться до температур выше 200 С.
- При печати ABS температуры достаточно чтобы тефлон начал выделять токсичные вещества, но его опасность по сравнению с опасностью самого ABS - не такая большая. ABS при плавлении выделяет ядовитый акрилонитрил и еще кучу всего, так что находиться в одном помещении с работающим принтером нельзя. Именно по этой причине я печатаю исключитльно PLA.
Если совсем не хочется иметь тефлон в хотенде - нужно смотреть в сторону цельнометаллических хотендов. Но они, как правило, громоздкие, дорогие и с активным охлаждением.
Насчет хотенда по вашей ссылке ничего сказать не могу. На картинке выглядит симпатично, можно попробовать.
Отправка комментария